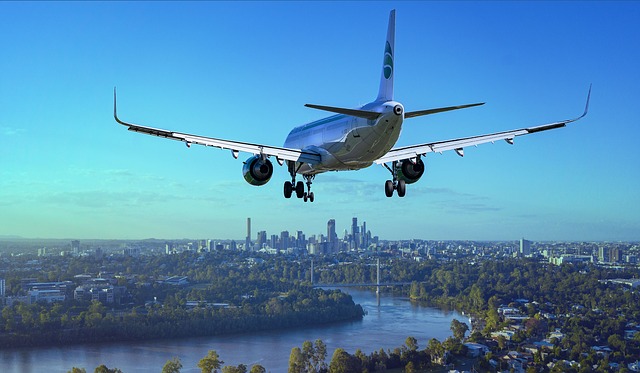
In This Episode…
In this episode I expand on the theme of continuous improvement by looking at the concept of LFE (Learning from Experience). I explain what it is by drawing on examples from the Nuclear and Aviation Industry.
Then I use a recent example from my own work where the application of Learning From Experience for a problem I had over nearly 4 years ago saved me over 2 hours of wasted time and frustration today.
Edited Transcript
Hi, this is Michael Tipper and welcome to today’s episode of the Profit Productivity Podcast.
In the last couple of episodes I have focused on talking about continuous improvement and spent one episode talking about a task I really detest doing. I shared how I improved my approach to the task by using the review, reflect and revise process.
In another episode I showed how I take that approach and apply it on a daily basis. I have two questions I ask myself at the end of every day. The first is “What was great about today? I use that for positive reinforcement and to ensure I keep doing the stuff that works.
Then I ask myself “What could I do differently to make the day even better?” This is about making changes to the things that didn’t work quite so well.
So that’s about continuous improvement and I want to expand that today by focusing on the concept of learning from experience (LFE).
Now I’ve spent the last eight years working in the nuclear industry. I have been embedded in one of the major nuclear providers in the country and have also worked as an external consultant with a number of other nuclear organisations over the last few years.
The Nuclear Industry has a concept called Opex (operational experience). It is one of the many mechanisms used by the industry to keep safety their number one priority for people.
Here’s what happens continuously. When something goes wrong, or even when something goes right, they raise what is known as a condition report (CR). It is raised when they believe something that’s happened or been discovered is worthy of note and capturing for future reference. They raise a CR and it goes into their operational experience system.
So let’s say there’s someone working on a particular valve in a particular plant and there is a problem with it and they’re not quite sure what it is. They will go to their operational experience database. They’ll put in the details and see what other people have done if they’ve had a similar experience.
That is how they’re able to transfer that knowledge across their industry. It’s a very powerful approach and when used properly saves time, saves the business money and certainly contributes to keeping their workforce safe.
Now, the nuclear industry isn’t the only industry that has a strong bias for continuous improvement and learning from experience. The aviation industry also do exactly the same. In fact, they’re probably the people who started using the approach in the first place. And the safety record in the aviation industry is second to none.
In fact, you may remember the story of Sully Sullenberger. There was a film about his story starring Tom Hanks. Sully was the captain of an Airbus A320 that lost thrust to both engines shortly after takeoff. The only place he could land was on the Hudson River.
That story went viral around the world and quite rightly so, him and his crew received all sorts of accolades.
The question to ask is how was he able to do that?
Well, first of all, he’s an outstanding pilots and at the time, had over 20,000 hours of flying experience. But it wasn’t just his flying experience that got him down safely. It was his extensive operational knowledge of what had happened in other similar situations.
His career is dominated by a focus on safety. In the US Air Force he had accident investigation duties. As an airline pilot, he was the local air safety chairman for the Airline Pilots Association. He knew Operational Experience relevant to the aircraft he was flying inside out because he was reading it on a regular basis.
In his mind he had a database of things he could call on in an emergency and that saved the plane and all its passengers.
Learning from experience is really important. But those are quite extreme examples. In the nuclear industry and the aviation industry something going wrong can be catastrophic which is why they do it.
I want to bring the principles back down to a much more trivial level and share my own example of operational experience from something that happened just a couple of days ago. I want to do that just to illustrate the principle because I think it’s something that we should all be aware of the benefits of doing so. Not only from a safety perspective, if that’s a line of work you’re in, but also from a time saving perspective.
Let me explain and set the scene.
When I’m recording interviews for my podcast, I use Skype on my Mac. In order to create broadcast quality audio, I use a R⌀de microphone interfaced into my Mac through a Line6 UX2 audio interface.
The details of the equipment don’t really matter. But to make the set up work, there’s a few drivers and software on the Mac that need to be in place for that to happen.
When I am doing a Skype call, I physically set up the microphone so it’s in front of me, I connect the Line6 UX2, open up the software, open up Skype and I am ready to go. It’s a two minute job to set up.
Three days ago I was due to record a call but when I opened up the software it came up with an error message – “Device, Not Authorised” and it wouldn’t work.
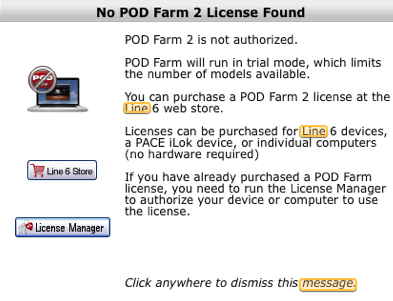
What did I do? Well let me take you back to 25th of September 2015 – three and a half years ago. On that day, exactly the same thing happened. I got the same annoying error message and spent two and a half hours trying to get the damn thing to work.
I had to do research on a number of different websites and forums. I had to read through the pdf documentation that came with the hardware and the software. I had to keep logging and and logging out of a members area I didn’t even know existed. It took me about two and a half hours, but eventually I fixed it.
That day I took screenshots, captured the steps I took as I solved the problem and created a detailed record of what I’d need to do if it even happened again in Evernote. The reason I know it happened on the 25th of September, 2015 because that’s when the, the note was created in Evernote.
So when it happened again a few days ago, I did a quick search in Evernote for “Line6 Error Message” and the note was at the top of the search results on my Mac. I quickly read it, saw what I had to do and in two minutes I had my system back up and running and I was ready to go.
I’ve had to do that twice since the 25th of September, 2015 and each time it’s only taken me two minutes to fix the problem.
Had I not bothered capturing my learning from experience at that time I would have had to go through the whole process of trying to find out how to do it all over again.
It probably would have taken me another two and a half hours. But it’s not only the lost time that is the downside, the additional stress and anxiety it would create would not help either. I can remember back in 2015 when I first fixed it, I was very frustrated. In fact several times in the note I have typed “Grrrrrrr”
But let’s focus on the positive. I now have a reference point where I can go back and find the solution to the problem quickly and easily. I know it’s likely it’s going to happen again because the problem has a history of repeating itself (probably to ensure their software is only used by authorised users).
I’ll just reiterate again what I’ve done with this example of my experience of Learning From Experience.
Nearly 4 years ago I had a problem that needed a solution. I put effort in to finding the solution. I captured the solution and put it into a system where I could easily find it again.
Although at the time it might have only taken maybe an hour and a half to solve it, I chose to put an extra 30 minutes in to capture the detail sufficiently so that I, or even someone else, could apply the same solution to the same problem.
That’s probably a good measure to have of the level of detail needed for something like this. Capture it so someone else could come and do it.
Someone else isn’t necessarily going to come and do it, but when you come back to read those notes months, maybe years later, you’re effectively someone else. So it has to be clear enough for you to go through as though you were doing it for the very first time
For me, by doing that, I was able to save time and more importantly, not get into an emotional funk because of it.
Life can be stressful as it is. We don’t live in a perfect world, but if we can smooth it in any way, shape, or form, I think that’s the good thing.
I strongly recommend you explore and capture your own learning experiences. Now it might not be a literal lifesaver, as in Sully’s case, but it might just be a time and stress saver for you.
So until tomorrow.